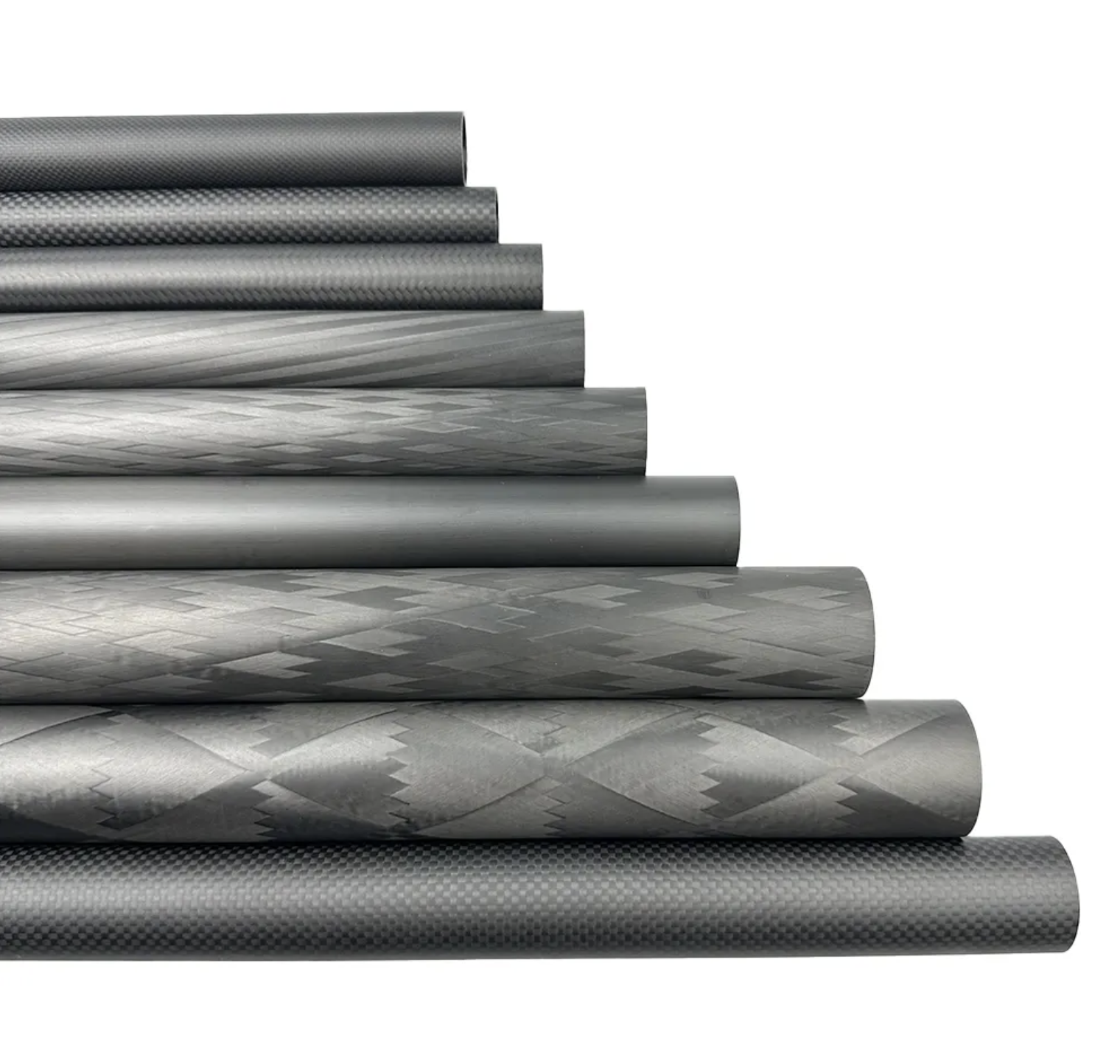
Here’s a detailed comparison between carbon fiber rolled tubes and filament-wound tubes in English, covering manufacturing processes, performance, applications, and more:
Manufacturing Process
Aspect | Rolled Tubes | Filament-Wound Tubes |
---|---|---|
Core Process | Layered wrapping of prepreg or dry fabric around a mandrel, followed by curing. | Automated winding of resin-impregnated fibers onto a mandrel at controlled angles (e.g., 0°, ±45°, 90°), then cured. |
Automation | Manual or semi-automated, simple setup. | Highly automated, requiring precision equipment for fiber tension and angle control. |
Fiber Orientation | Limited to axial or hoop directions. | Multi-angle fiber alignment for optimized strength and stiffness. |
Shape Flexibility | Best for simple cylindrical shapes. | Suitable for complex geometries (e.g., tapered, irregular cross-sections). |
Performance Comparison
Property | Rolled Tubes | Filament-Wound Tubes |
---|---|---|
Mechanical Strength | High axial strength but weak hoop strength; prone to delamination. | Balanced axial/hoop strength; superior compressive/torsional resistance. |
Anisotropy | Highly anisotropic (direction-dependent). | Reduced anisotropy via multi-angle layering. |
Weight Efficiency | Moderate (uneven wall thickness). | Excellent (uniform fiber distribution, precise wall thickness control). |
Fatigue Resistance | Lower (weak interlayer bonding). | High (continuous fibers, strong interlayer adhesion). |
Cost & Production
Factor | Rolled Tubes | Filament-Wound Tubes |
---|---|---|
Equipment Cost | Low (simple tools or manual). | High (specialized winding machines, tension systems). |
Production Cost | Low for small batches. | High initial cost, but cost-effective for large volumes. |
Production Speed | Fast (simple curing process). | Slower (precision winding and curing). |
Scalability | Limited to small-scale production. | Ideal for mass production. |
Applications
Field | Rolled Tubes | Filament-Wound Tubes |
---|---|---|
Industrial | Decorative parts, lightweight frames, drone arms. | High-pressure tanks, pipelines, robotic arms. |
Aerospace | Non-load-bearing components (e.g., interior brackets). | Rocket motor casings, aircraft landing gear. |
Sports Equipment | Low-cost fishing rods, tent poles. | High-end bicycle frames, yacht masts. |
Energy | — | Hydrogen storage tanks, wind turbine spar tubes. |
Selection Guide
- Choose Rolled Tubes:
- Budget constraints.
- Low-volume customization.
- Non-critical structural applications (e.g., aesthetics, lightweight frames).
- Choose Filament-Wound Tubes:
- High-performance load-bearing applications.
- Complex fiber orientation requirements.
- Mass production with strict quality control.
Leave A Comment